Maintenance Practices for Ensuring Longevity of Inverter VFDs
Understanding Inverter VFD Components and Operation
Rectification, Filtering, and Inversion Processes
Understanding the inverter VFD components begins with the rectification process, which converts alternating current (AC) to direct current (DC). This stage is critical as it utilizes diodes and rectifier circuits to ensure that the current transitions smoothly. Diodes play a vital role by allowing the current to flow in a single direction, facilitating a stable DC conversion. Next, the filtering process comes into play, ensuring the reliability of the direct current produced. Capacitors serve a crucial function here by smoothing out the DC output, effectively minimizing voltage ripples and enhancing the overall performance of the frequency drive.
Following filtering, the inversion process is engaged to convert the direct current back to alternating current at a specific frequency and voltage, crucial for driving efficient motor operations. Insulated Gate Bipolar Transistors (IGBTs) are the stars of this process, allowing precise control over both voltage and frequency. They are integral in ensuring that the converted AC is suitable for the motor's operational needs, noticeably enhancing the drive’s efficiency in various industrial applications.
Role of Control Circuits and Feedback Systems
Control circuits in an inverter VFD are indispensable as they regulate the output frequency and voltage delivered to the motor. These circuits ensure that the motor operates within desired parameters, thereby optimizing performance and extending the equipment's lifespan. Meanwhile, feedback systems, including sensors and encoders, provide real-time data that is crucial for maintaining optimal performance. These systems monitor the motor's operational status and relay necessary adjustments to the control circuit for precision and efficiency.
The significance of Proportional-Integral-Derivative (PID) control cannot be overstated when it comes to achieving precise speed control. In various applications, PID control is utilized to fine-tune speed by processing data from feedback systems. This ensures that speed deviations are quickly corrected, resulting in smoother operations and effective energy use, particularly in challenging environments where exact speed control is necessary.
Impact of Single to Three Phase VFD Configurations
The shift from single to three phase VFD configurations can significantly impact power delivery and efficiency in industrial settings. Single to three phase configurations distribute electrical loads more evenly, reducing strain on individual phases and enhancing the VFD's capacity to handle larger workloads efficiently. This transition can yield impressive efficiency improvements; in some cases, facilities have reported up to a 10% increase in energy efficiency when using three-phase systems.
Converting single-phase to three-phase VFDs is particularly beneficial in industrial applications where power demand is high. By adopting this setup, businesses can experience substantial cost savings over time due to improved efficiency and reduced power wastage. Thus, embracing these configurations not only enhances system reliability but also offers an economically viable solution for industries looking to optimize their energy consumption.
Essential Maintenance Practices for Inverter VFDs
Regular Inspection for Overheating and Loose Connections
Conducting regular inspections for overheating and loose connections is crucial for maintaining the optimal performance of inverter VFDs. Overheating can lead to serious failures in the drive, potentially causing costly downtime. Regularly checking the system for signs of excess heat can help identify issues early. Here are some best practices:
- Inspect the cooling systems for obstructions in heatsinks and fans, ensuring the VFD operates efficiently.
- Examine electrical connections and secure them according to the OEM's torque specifications. Loose connections can lead to power losses and faults.
- Evidence from industry experts suggests that regular inspections can significantly extend the average lifespan of VFD systems, often improving longevity by up to 30%.
Cleaning Dust and Ensuring Proper Ventilation
Routine cleaning and proper ventilation are key to preventing dust buildup, which can compromise cooling efficiency and lead to overheating. Dust can obstruct air filters and cooling fans, reducing the performance of VFDs. Therefore, ensuring adequate ventilation pathways is essential for optimal air circulation.
- Dust build-up: Regular cleaning of enclosures and filters prevents these issues and maintains cooling efficiency.
- Ventilation: Ensure pathways around VFD installations are clear to allow sufficient airflow.
- Actionable tips: Implement a monthly cleaning schedule, checking for dust accumulation and obstructions in cooling systems to sustain peak efficiency.
Monitoring Frequency Drive Phase Converter Efficiency
Monitoring the efficiency of frequency drive phase converters ensures better overall system performance. Regular efficiency assessments can reveal areas for improvement, leading to energy savings.
- Use metrics and tools like power meters and thermal imaging to monitor drive frequency performance.
- Data on energy savings shows that routine efficiency monitoring can reduce energy consumption by up to 15%.
- By staying ahead of efficiency challenges, operators can enhance system reliability and maintain cost-effective energy usage.
Implementing these maintenance practices can optimize the performance and extend the life of inverter VFDs, supporting long-term operational efficiency.
Addressing Common Causes of VFD Failure
Preventing Electrical Surges and Voltage Fluctuations
Electrical surges and voltage fluctuations are primary culprits behind VFD component damage. Surges can stem from external factors like lightning or internal issues such as electrical faults. These inconsistencies impose significant stress on VFD circuits, often leading to immediate component failure. To shield VFDs from such fluctuations, one should employ surge protectors and filters. These devices serve as vital barricades, absorbing and mitigating the impact of power spikes. By integrating effective protective measures, failure rates can be minimized, ensuring longer operational life for the VFD systems.
Mitigating Component Wear in Variable Frequency Drive Systems
Component wear is an inevitable aspect of maintaining VFD systems, with key elements like capacitors and Insulated-Gate Bipolar Transistors (IGBTs) being particularly vulnerable. Regular monitoring of these components is crucial to identify signs of wear before they lead to more extensive damage. Implementing strategies such as temperature control and balanced loading can significantly extend the lifespan of these parts. Preventative maintenance plays a pivotal role in avoiding hefty repair costs and system downtimes. By proactively replacing worn components, one not only saves on repair costs but also ensures the consistent performance of VFD systems.
Avoiding Overloading in Single to 3 Phase VFD Setups
Overloading in single to three phase VFD setups can drastically hinder performance and undesirable shorten system lifespan. Consistent overloading results in overheating and potential irreversible damage to the drive and connected motors. To avert this, it is essential to select a VFD size that matches the load requirements accurately. Utilizing tools and consulting with experts can assist in proper sizing, preventing unnecessary strain. Real-world examples have shown that aligning VFDs with specific load demands fosters efficient operation and lower energy consumption, ultimately optimizing the system’s overall effectiveness.
LCGKVFD Product Solutions for Reliable Operation
LC520 Frequency Converter for Elevator Applications
The LC520 Frequency Converter is specifically designed to enhance the operational reliability in elevator applications. This converter boasts unique features like advanced microcontroller technology that optimizes performance, ensuring smooth acceleration and deceleration phases critical for elevators. It meets high efficiency ratings and safety certifications, underscoring its reliability during operations. With integration capability that allows seamless connection with existing elevator systems, installation of the LC520 is straightforward, reducing potential downtime and complexity. These traits make it an indispensable product for elevators aiming for enhanced efficiency and long-term operational stability.
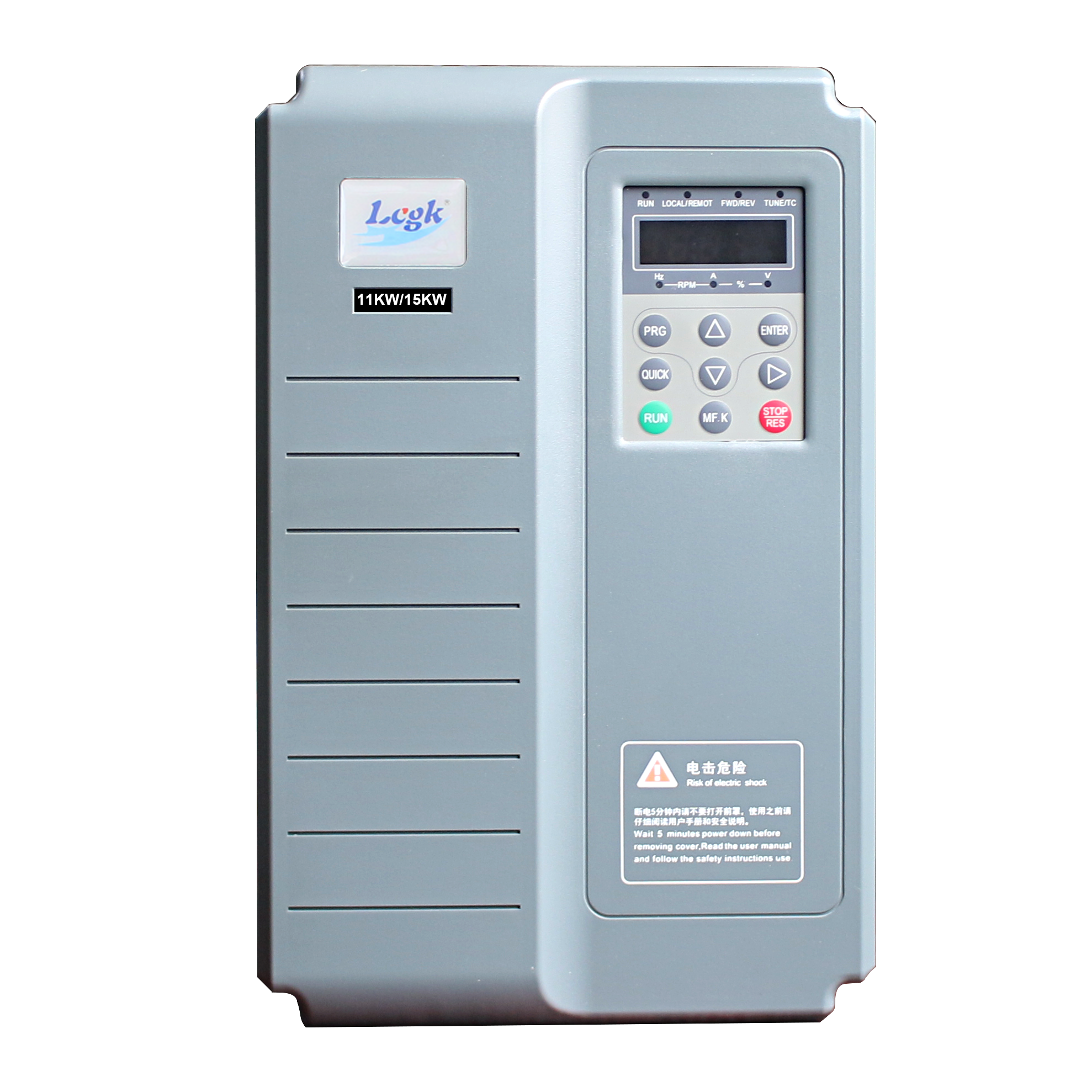
LCJ20 Kitchen Fan-Specific Frequency Converter Features
The LCJ20 Frequency Converter stands out with features tailored for kitchen fan applications, promising significant energy savings and efficiency gains. Designed explicitly for kitchen fans, it aids in reducing energy consumption by adjusting fan speeds based on real-time demand, enhancing kitchen ventilation systems crucial for maintaining indoor air quality. This converter is vital for kitchens as it provides a tailored solution, ensuring optimal fan operation, and contributing to reduced operating costs. By implementing specific frequency converters like the LCJ20, businesses can greatly benefit from improved ventilation systems and reduced energy expenditure.
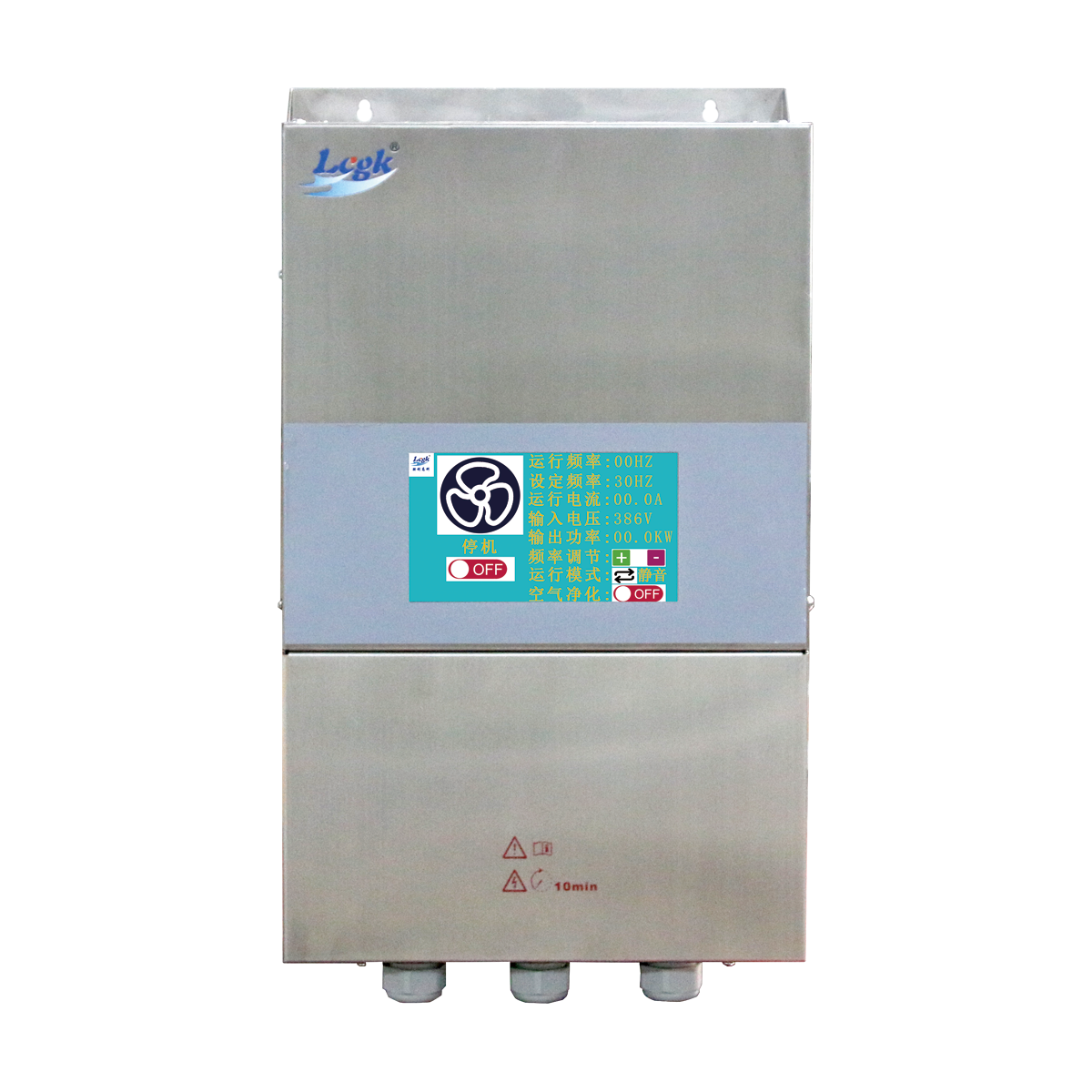
LP300Y Permanent Magnet Synchronous Controller Benefits
The LP300Y Permanent Magnet Synchronous Controller is equipped with advanced functionalities to deliver superior energy efficiency for synchronous motors. This controller stands out by minimizing energy losses and optimizing motor performance compared to traditional controllers. For instance, industries using the LP300Y have reported substantial improvements in application areas like conveyor systems and specialized machinery, showcasing its capability to significantly enhance operational efficiency. With real-world applications demonstrating marked energy reductions, the LP300Y emerges as a pivotal asset for industries focused on sustainable and efficient motor operations.
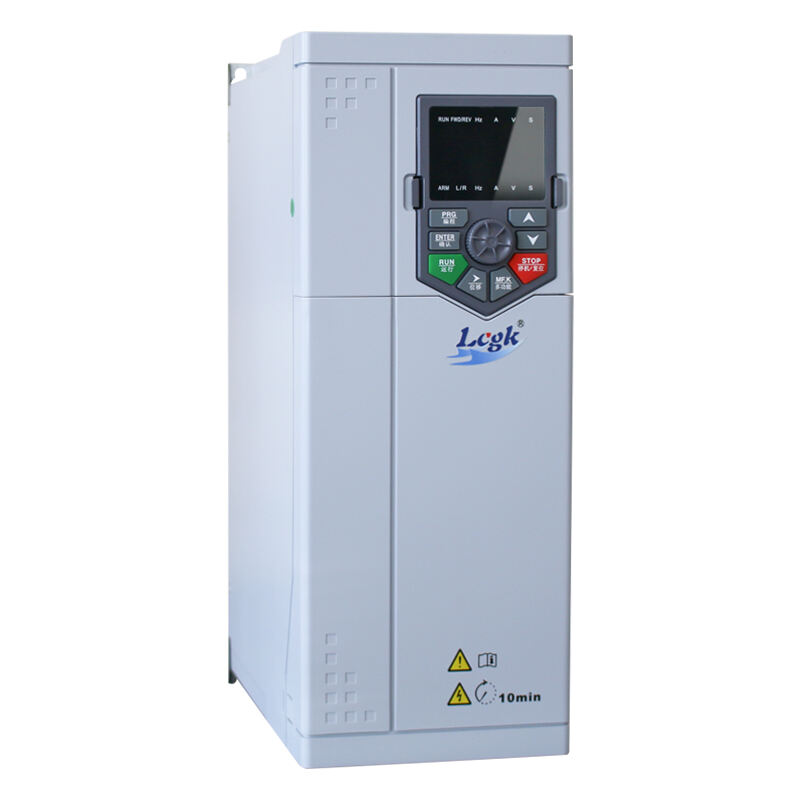
Advanced Protection Strategies for VFD Longevity
Installing Surge Protection Devices for Phase Converters
Surge protection devices are crucial in safeguarding phase converters against voltage spikes, which can cause significant damage and operational failures. These devices operate by diverting excess voltage away from sensitive components in the converters, thus protecting them from harmful surges. When selecting and installing surge protectors, it is best practice to ensure compatibility with the specific requirements of your VFD systems. This entails evaluating the protection rating of the device, grounding it effectively, and positioning it close to the VFD to maximize efficiency. Statistics reveal that the failure rates of VFDs reduce significantly – by as much as 50% – when proper surge protection is employed, enhancing overall system reliability.
Reducing Electromagnetic Interference (EMI) Risks
Electromagnetic interference (EMI) in VFD systems can originate from sources like unshielded cables, inadequate grounding, and the close proximity of electronic devices. This interference adversely affects VFD performance, causing erratic operations and communication errors. To mitigate EMI risks, implementing strategies such as proper cable management and using shielded cables is recommended. Additionally, ensuring all electronic equipment is grounded can help reduce these risks. Data indicates that robust EMI mitigation tactics can lead to a 30% decrease in maintenance costs and significantly reduce operational downtimes, thus promoting a smoother and more reliable VFD operation.
Updating Software for Variable Frequency Drive Optimization
Regular software updates play a vital role in optimizing VFD performance and ensuring system security. They provide the latest enhancements and security patches that help in maintaining peak VFD efficiency. The process of updating software should include a structured approach to verify that all systems run the latest versions, involving regular audits and compliance checks. An example of successful software-related improvements is seen in optimizations that result from algorithm upgrades, which can enhance processing speeds by up to 20% and secure communications against emerging threats. These enhancements lead to reduced system faults and improved operational efficiency.
Establishing Effective Maintenance Routines
Scheduled Calibration of Single Phase to Three Phase VFDs
Regular calibration of single phase to three phase VFDs is crucial to ensure accurate performance and optimal efficiency. Calibration helps in aligning the VFDs with their operational parameters, which maintains system accuracy and avoids unnecessary energy consumption. It's beneficial to maintain a checklist that includes calibration procedures, recommended intervals, and specific calibration points. Generally, VFDs should be calibrated quarterly to align with the dynamic demands of industrial applications.
Following this routine can substantially improve the performance and lifespan of the VFDs. According to industry studies, regular calibration reduces system errors by more than 20%, ensuring that operations run smoothly and efficiently. By keeping the calibration process organized and systematic, businesses can expect not only improved accuracy but also enhanced energy efficiency and reduced operational costs.
Documenting Error Logs and Performance Metrics
Maintaining detailed error logs and performance metrics is essential for the effective troubleshooting and regular maintenance of VFD systems. Error logs facilitate rapid diagnosis and resolution of issues, minimizing downtime. Meanwhile, documenting key performance metrics, such as operational efficiency, voltage levels, and load capacity, provides insights into system health and performance trends over time.
For instance, a case study highlighted a manufacturing plant that implemented systematic documentation, resulting in a 30% reduction in troubleshooting time and a significant decrease in downtime. By understanding and tracking these metrics, businesses can foresee potential issues and take preemptive actions. Systematic documentation helps companies maintain higher efficiency levels and longer equipment life cycles.
Partnering with Certified Technicians for Complex Repairs
Partnering with certified technicians is vital for addressing complex VFD issues, ensuring reliability, and extending the service life of VFDs. Certified professionals bring specialized knowledge and skills to handle intricate repairs that can otherwise risk system stability if managed improperly. When selecting technicians for VFD servicing, it is crucial to verify credentials, past experience, and proficiency in specific VFD brands and models.
Engaging qualified professionals not only enhances repair quality but also boosts overall system reliability. For instance, one industrial facility saw its VFD system reliability improve by 25% after shifting maintenance responsibilities to certified technicians. Ensuring that repairs are handled by experts helps avoid costly mishaps and reinforces long-term operational stability.