Advantages of Integrating Inverter VFDs into Conveyor Systems
Key Advantages of Using Inverter VFDs in Conveyor Systems
Precision Speed Control for Enhanced Material Handling
Inverter Variable Frequency Drives (VFDs) are pivotal in achieving precision speed control for conveyor systems, making them essential for material handling applications where timing and speed are critical. By fine-tuning speed parameters, VFDs allow for real-time adjustments based on the varying weights and types of materials conveyed, thereby boosting operational efficiency. This technology facilitates smoother operation with reduced wear on mechanical components. Research indicates that enhanced speed control can decrease material spillage by up to 30%, underscoring its significance in maintaining a streamlined workflow.
Soft Start Functionality to Reduce Mechanical Stress
The soft start functionality of inverter VFDs plays a crucial role in minimizing mechanical stress on conveyor systems. By allowing gradual acceleration, it effectively reduces initial torque and mechanical shock to components. This capability significantly cuts the risk of premature wear and tear on motors and belts; manufacturers often report reductions in mechanical failures of up to 50% with the use of soft starters. The ability to extend the lifespan of equipment through reduced mechanical stress is a key advantage, promoting safer operations and sustained productivity.
Energy Optimization Through Variable Torque Management
Inverter VFDs offer remarkable energy optimization through variable torque management, dynamically adjusting their output based on load requirements. This adaptability leads to significant energy savings and reduced operational costs, making it a prudent investment for long-term efficiency. Reports suggest that such energy optimization can achieve savings of 20-50% on energy bills for conveyor systems. The ability to manage energy consumption efficiently not only ensures cost savings but also aligns with sustainable practices, making inverter VFDs a smart choice for modern industries.
Energy Efficiency & Cost Savings with VFD Technology
AC to DC Conversion for Adaptive Power Distribution
Opting for AC to DC conversion in conveyor systems can significantly enhance energy distribution efficiency, meeting the specific power requirements of the application. This conversion process minimizes energy losses that occur during transmission and is especially beneficial in high-demand environments, ensuring optimized performance. Research indicates that industries implementing AC to DC converters have seen energy cost savings of 20% or more for large-scale installations. This adaptability is crucial for sustainable operations in sectors where energy use is a substantial part of operating costs.
Frequency Drive Adjustments Based on Load Demand
Variable Frequency Drives (VFDs) are designed to intelligently adjust their output according to actual load demand, thus enhancing operational efficiency without unnecessary energy expenditure. This adaptability leads directly to cost savings, as it ensures energy is only used in accordance with the operational requirements rather than continuously running at full capacity. Demonstrations across various industrial applications have shown that frequency drive adjustments can reduce energy waste by about 30%, making it a financially savvy choice for businesses aiming to improve energy management.
Reduced Power Consumption in Single/Three-Phase Systems
VFDs play a crucial role in minimizing power consumption by efficiently managing energy flow in both single and three-phase systems. This technology permits flexible installations across different environments while maintaining energy efficiency, aligning with diverse power needs. Experts have reported an average reduction of up to 40% in energy consumption when industries switch from traditional systems to VFD technology. This significant decrease not only cuts operational costs but also supports sustainability goals, providing an additional rationale for investing in modern VFD solutions for industrial applications.
Motor Protection & Extended Equipment Lifespan
Mitigating Common Mode Voltage (CMV) Risks
Common Mode Voltage (CMV) poses significant challenges to motor insulation and bearing integrity. Variable Frequency Drives (VFDs) offer robust solutions to mitigate these risks through their advanced design features that focus on reducing electrical stress. By integrating CMV suppression techniques, motors can experience enhanced longevity, leading to longer service life and reduced maintenance costs. Industry studies show that companies implementing effective CMV management can see up to a 25% improvement in motor life expectancy.
Shaft Grounding Solutions for Bearing Protection
Shaft grounding is essential for protecting bearings from electrical discharge, which can lead to premature motor failure. VFDs often include shaft grounding measures to counteract this issue. Implementing these solutions significantly cuts down on maintenance expenses related to bearing replacement and lengthens service intervals. Many manufacturers have reported a more than 30% reduction in bearing failures upon incorporating shaft grounding solutions into their systems.
Surge Suppression in Long-Distance Conveyor Applications
Incorporating surge suppression technology is vital in protecting motors from voltage spikes, which are particularly common in extensive conveyor systems. This technology prevents costly motor damage and minimizes the risk of unexpected downtime due to electrical failures. Case studies reveal that employing surge suppression can reduce electrical faults by 40% or more, making it a critical feature in safeguarding investments in long-range conveyor applications.
Top Inverter VFD Models for Conveyor Systems
LC410 High-Performance Vector Frequency Converter: Precision & Reliability
The LC410 High-Performance Vector Frequency Converter is renowned for offering precision control that ensures optimal performance in demanding conveyor applications. Industries that require high operational demands often turn to the LC410 due to its robust design that prioritizes reliability and long service life. Customer testimonials frequently highlight improvements in throughput and reduced downtime after integrating the LC410 into production lines. You can learn more about the LC410 in greater detail.
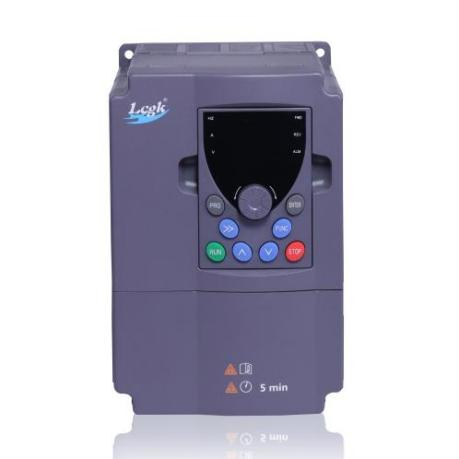
LFZ400Y VFD for Heavy-Duty Textile & Conveyor Integration
Specifically engineered for heavy-duty environments, the LFZ400Y VFD offers both durability and adaptability for textile and conveyor applications. With advanced torque management capabilities, it operates efficiently even in challenging conditions, driving operational excellence. Industry reports indicate that facilities utilizing the LFZ400Y experience a marked reduction in operational failures and maintenance costs. For more detailed information, please visit LFZ400Y Type VFD for Textile Machinery.
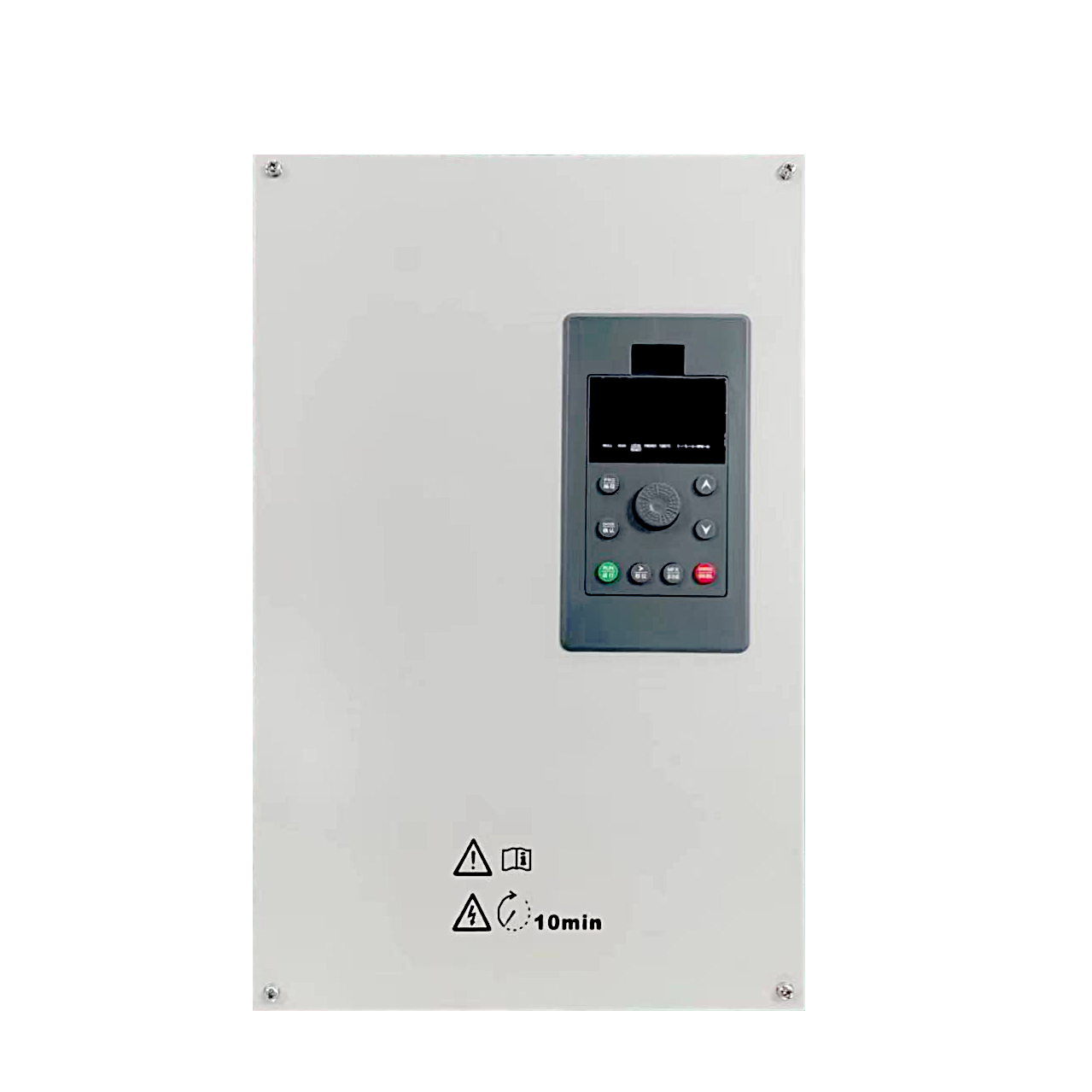
LG300A 690V Cabinet-Type Converter for Industrial Power Demands
The LG300A 690V Cabinet-Type Converter is designed to meet the needs of high voltage industrial power demands, providing a compact yet highly effective solution without compromising on performance. This model supports a variety of operational functions, making it versatile for numerous industrial applications. According to review data, operations running the LG300A have reported efficiency gains and in some cases, energy savings of over 25%. To explore the LG300A further, you can visit LG300A 690V Input Cabinet Type Strong Power Vector Frequency Converter.
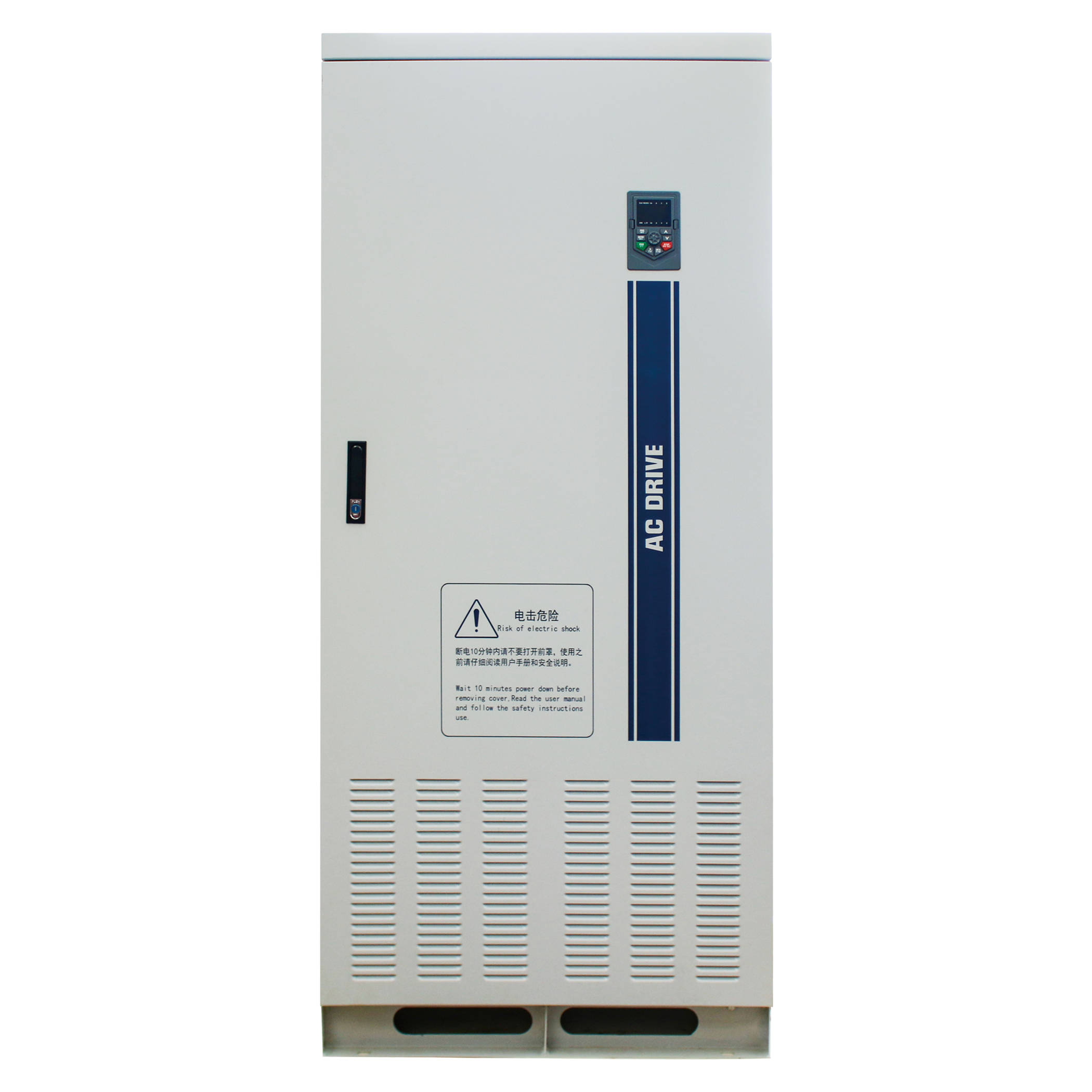
Industry Applications & Performance Case Studies
Mining: Synchronized Speed Control for Ore Transport
In the mining industry, the integration of VFDs for synchronized speed control is crucial to ensure a steady and uninterrupted transportation of ore. This meticulous control enhances production rates by minimizing waste typically caused by fluctuating transportation speeds. According to case studies, mining operations utilizing VFDs experience up to 40% increase in output efficiency. By adjusting the power frequency and voltage, VFDs not only optimize the operational performance but also contribute significantly to reducing wear and tear on mining equipment, leading to decreased downtime and maintenance costs.
Packaging: Adaptive Belt Speeds to Minimize Product Waste
In packaging operations, VFDs are leveraged to adjust conveyor belt speeds, aligning them seamlessly with production line requirements to minimize product waste. This adaptability promotes smoother workflows and reduces spoilage resulting from improper handling speeds. Statistics reveal that implementing adaptive belt speeds in packaging facilities can lower waste by as much as 35%, thus enhancing overall profitability. By offering precise control over motor speeds, VFD technology optimizes packaging processes, allowing for real-time adjustments that boost operational efficiency and quality assurance.
Renewable Energy: VFD-Driven Conveyors in Solar Panel Production
VFD technology is increasingly becoming indispensable in the renewable energy sector, especially within solar panel production, where precision is paramount. These drives optimize material handling rates, ensuring that they align with the actual production demand, thereby paving the way for sustainable manufacturing practices. Performance case studies indicate that integrating VFDs into solar panel processes improves production efficiency by up to 30%. The precise speed control offered by VFDs enhances the throughput process, leading to increased yields and more efficient use of installed equipment.
By examining these industry applications and case studies, it becomes evident that VFDs play a pivotal role in enhancing efficiency across various sectors. From mining to packaging and renewable energy, the adaptive capabilities of VFDs address distinct operational challenges, ultimately facilitating improved productivity and cost savings.
Implementing VFDs: Installation & Maintenance Best Practices
Proper Grounding for Electrical Stability
Proper grounding is essential for ensuring electrical stability in Variable Frequency Drive (VFD) installations. It plays a crucial role in safeguarding systems from electrical surges and transients, which can cause significant disruptions. By adhering to established grounding protocols, we can effectively mitigate issues related to electrical noise, ensuring smoother and more stable operations for our systems. Following these practices is paramount, considering that approximately 70% of electrical interference problems can be addressed through appropriate grounding techniques, enhancing overall system reliability.
PID Loop Calibration for Process Synchronization
PID loop calibration is a vital aspect of maintaining optimal system performance, ensuring that processes respond accurately to varying loads. This calibration facilitates precise adjustments in speed and torque, which is crucial for optimizing process synchronization. By doing so, we enhance the efficiency and reliability of conveyor systems, allowing for seamless operations. Experts in the field recommend conducting regular PID loop recalibrations to uphold high performance levels. This proactive approach helps in maintaining the desired process control and prevents potential discrepancies in operations.
Thermal Management in High-Cycle Operations
Effective thermal management is crucial for the longevity and efficiency of VFD systems, especially when dealing with high-cycle operations. Implementing robust cooling solutions and routinely checking for thermal efficiency can prevent system overheating and subsequent failures. Data indicates that proper thermal management practices can increase equipment lifespan by up to 25%, significantly reducing maintenance costs and enhancing sustainability. By focusing on these strategies, we ensure the reliable functioning of VFD systems, even in demanding operational environments.